In today's world, safety is paramount, especially in industries with prevalent hazards and risks. Safety checklists are crucial in minimizing risks, ensuring compliance, and promoting a safe work environment. This article provides an in-depth exploration of the meaning and significance of safety checklists in health and safety. We will delve into their purpose, key components, benefits, development, and implementation, focusing on their importance in healthcare and other industries where safety is paramount.
What is a Safety Checklist?
A safety checklist is designed to systematically assess and verify compliance with safety protocols, procedures, and regulations. It provides a structured approach to identify potential hazards, evaluate risks, and ensure that critical safety measures are implemented and adhered to. Safety checklists promote consistency, efficiency, and thoroughness in inspections and assessments, allowing organizations to manage risks and enhance safety practices proactively.
Key Components of a Safety Checklist
To be effective, a safety checklist should include several key components:
Comprehensive Coverage
An effective safety checklist should encompass many safety protocols, procedures, and guidelines relevant to the specific industry and work environment. It should cover various areas, including patient safety, surgical safety, inspection of equipment and machinery, electrical safety, and compliance with industry regulations. The checklist should be tailored to the specific hazards and risks present in the industry or workplace to ensure its relevance.
Clear and Concise Format
The checklist should be designed in a clear and concise format that is easy to understand and navigate. Each item on the checklist should be clearly stated, with specific instructions and requirements. A well-structured checklist helps users easily identify and assess potential hazards and facilitates consistent and accurate documentation.
Specificity
The checklist should include detailed and specific items to ensure thorough inspections and assessments. Each item should clearly outline what needs to be evaluated, assessed, or implemented. Specificity helps capture important details and ensure that critical safety measures are not overlooked.
Relevance to the Workplace
A safety checklist should be tailored to the industry or workplace's specific hazards, risks, and work processes. It should address the unique challenges and safety concerns within the organization. By ensuring the checklist is relevant to the workplace, organizations can effectively assess and manage the risks associated with their specific operations.
Benefits of Using Safety Checklists
Implementing safety checklists offers several benefits to organizations:
Improved Compliance
Safety checklists serve as a tool to ensure compliance with safety protocols, procedures, and industry regulations. By systematically following the checklist, organizations can verify that all necessary safety measures are implemented correctly. Compliance with safety guidelines and regulations helps reduce the likelihood of accidents, injuries, and regulatory penalties.
Enhanced Communication
Safety checklists facilitate clear communication and understanding among team members regarding safety expectations and procedures. They provide a standardized format for documenting safety-related information and enable efficient information sharing. The checklist is a reference point for all safety inspection and assessment stakeholders, fostering effective communication and collaboration.
Consistency and Thoroughness
Safety checklists promote consistency in safety inspections, assessments, and audits. They provide a structured framework that ensures all necessary steps are taken to identify hazards, evaluate risks, and implement control measures. The checklist is a reminder to assess each aspect thoroughly, minimizing the chance of overlooking critical safety measures.
Efficiency and Time Savings
By streamlining the inspection process, safety checklists help save time and resources while maintaining high safety standards. The checklist serves as a guide, ensuring that inspections and assessments are conducted efficiently and effectively. It helps inspectors focus on relevant aspects and ensures no critical steps or safety measures are missed. Safety checklists promote efficiency, allowing organizations to allocate their resources effectively, leading to time and cost savings.
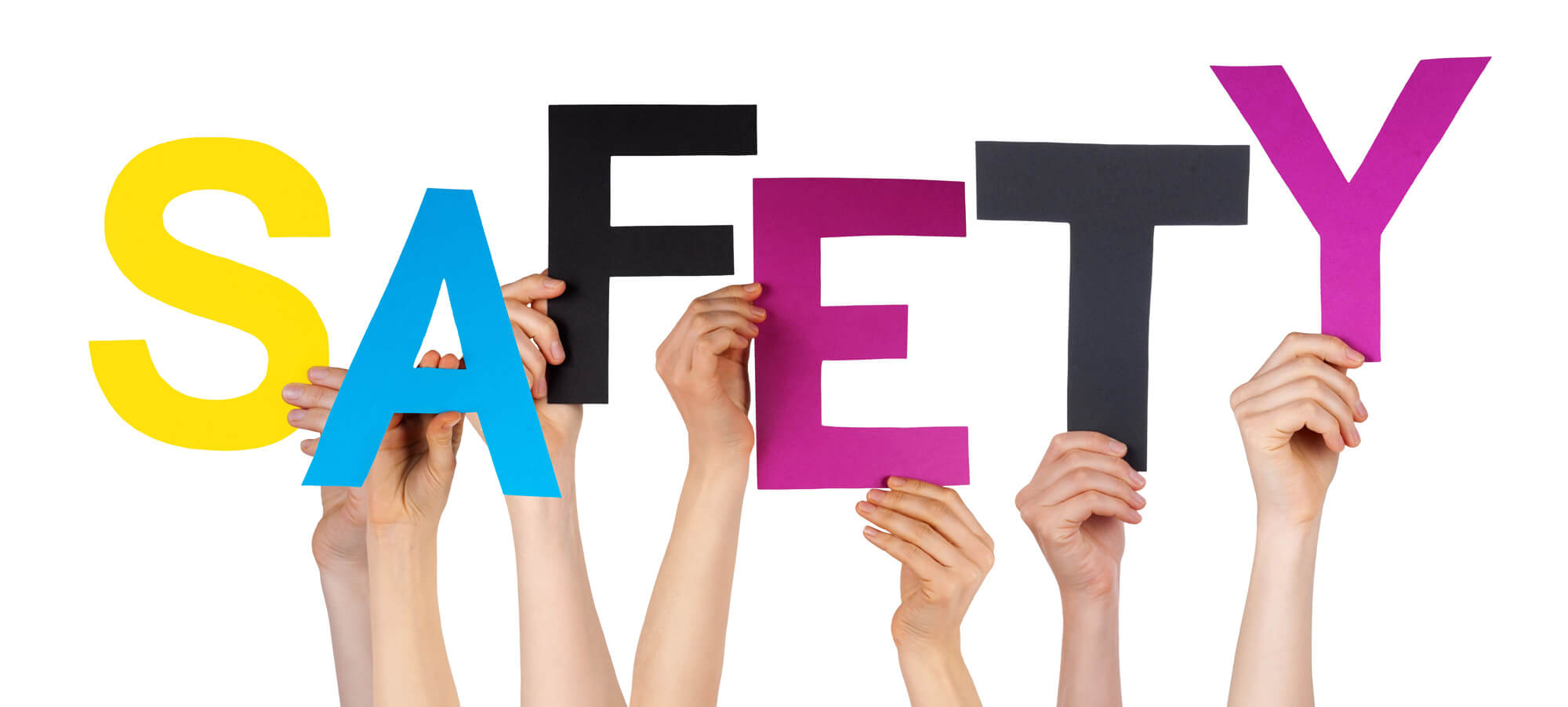
Developing an Effective Safety Checklist
To develop an effective safety checklist, organizations should consider the following:
Identify Applicable Regulations and Guidelines
Identifying and incorporating relevant safety regulations, guidelines, and industry best practices into the checklist is essential. This ensures that the checklist aligns with the specific requirements and standards applicable to the industry or workplace.
Consultation with Subject Matter Experts
Developing the checklist involves subject matter experts, such as safety professionals and experienced workers. Their expertise can provide valuable insights into potential hazards, risks, and control measures specific to the industry. Organizations can collaborate with experts to ensure the checklist's comprehensiveness and relevance.
Regular Review and Updates
Safety checklists should be regularly reviewed and updated to reflect changes in safety regulations, procedures, and industry standards. Regular evaluation helps organizations stay updated with emerging safety trends and implement the most effective control measures. It also allows for continuous improvement and refinement of the checklist based on feedback and lessons learned.
Implementing Safety Checklists in the Workplace
To successfully implement safety checklists in the workplace, organizations should consider the following strategies:
Training and Familiarization
Employees should receive proper training on how to effectively use the checklist and understand its importance in promoting safety. Training programs should cover the purpose of the checklist, how to complete it accurately, and the significance of complying with safety measures. Familiarizing employees with the checklist and its application fosters a safety culture and ensures effective implementation.
Integration with Work Processes
Integrating the safety checklist into existing work processes is vital for successful implementation. The checklist should be a routine part of safety inspections, assessments, and operational procedures. By seamlessly integrating the checklist into work processes, organizations can ensure that safety considerations are consistently addressed and prioritized.
Continuous Improvement
Safety checklists should be viewed as dynamic tools that require continuous evaluation and improvement. Organizations should encourage feedback from users and stakeholders to identify areas of improvement and update the checklist accordingly. By fostering a culture of continuous improvement, organizations can enhance the effectiveness of safety checklists and stay proactive in managing hazards and risks.
Conclusion
Safety checklists are powerful tools for promoting workplace safety, minimizing risks, and ensuring compliance with safety protocols and regulations. Organizations can systematically assess hazards, evaluate risks, and implement control measures by incorporating a comprehensive and well-designed checklist into their safety management practices. Safety checklists enhance communication, consistency, and efficiency in safety inspections and assessments, leading to improved compliance, reduced incidents, and a safer work environment. Let us prioritize using safety checklists to safeguard the well-being of employees and create workplaces that prioritize safety and compliance.